Tin Tức
Wei Hongyun 丨 Portable remote teaching system for machine tools
“Remote teaching” has applications in many fields, the most common of which is medical surgery. Through the remote teaching system, the operating images in the operating room and the vital signs data of the patients are transmitted to the teaching room on the other end of the network in real time.
Through this technical means, two tasks can be achieved:
First, remote demonstration: the instructor in the operating room, through the live teaching system of the remote teaching system, to demonstrate the surgical process to students in the classroom or to study and study colleagues. This situation is also called distance learning.
Second, remote guidance: the instructor in the classroom, through real-time acquisition of the scene of the surgery and the patient’s vital signs parameters, at any time comprehensively judge the condition, give surgical guidance, and feedback to the language through the remote teaching system Peer performing surgery in operating room. This situation is also called remote consultation, because there may be more than one instructor in the classroom, but a consultation team composed of multiple experts. This remote consultation mode is particularly suitable for situations where high-level doctors are lacking on the scene in remote areas and battlefield hospitals, but it is difficult or impossible for patients to move.
So what does this medical remote teaching system have to do with our machine tool field?
If you are a machine tool user, do you think that when a machine tool fails, it is no different from a “patient”? Also, is it a “patient” that is difficult to move?
If you are the technical support of a machine tool factory, every time you promote a new model of machine tool, customer training must be a hard work. Regardless of whether it is taught or learned, one person must travel on business to meet the other. Sometimes in order to solve a small problem, or even to clarify a small misunderstanding, it really takes more than half a day, and you have to pay for gasoline-maybe customers think you are too slow.
So can we also build a remote teaching system for machine tools?
You can use the CNC system of Weihong Co., Ltd. (stock code: 300508)! The newly released Weihong CNC system products have integrated “Weihong Cloud-Remote Assistance” function. On the premise that the machine tool is connected to the Internet, as long as the “remote assistance” function is enabled, remote users can directly log in to the CNC system interface, and not only can view the real operation interface in real time, but also perform remote operations. Then how to deal with the voice and video signals of the personnel on both sides to understand and understand the situation on site? It’s very simple, because there are already many tools for video calls on everyone’s mobile phones, such as WeChat video calls, iPhone facetime, and so on.
Wei Hongyun’s remote assistance plus mobile phone video calls, these handy tools can meet the following scenarios:
First, remote teaching and demonstration: the technical support staff of the machine tool factory allows customers to log in remotely to the machine tool they use as a demonstration, Then make various demonstration actions or let the user experience the operation. At the same time, video calls can be used to explain and demonstrate the work of the mechanical part of the machine tool.
Second, remote guidance and diagnosis: machine tool users allow machine tool factory technical support personnel to remotely log in to their own machine tools, and then both parties use mobile phone video calls to communicate between personnel. Users can elaborate their own problems, and technical support can directly view and operate the machine tool after remote login at any time, and even change software and parameter configuration. If you need to check the movement of the on-site machine tool and the processing of the workpiece, you can request the user to cooperate with the mobile phone video communication to transfer the on-site images of the machine tool and the workpiece.
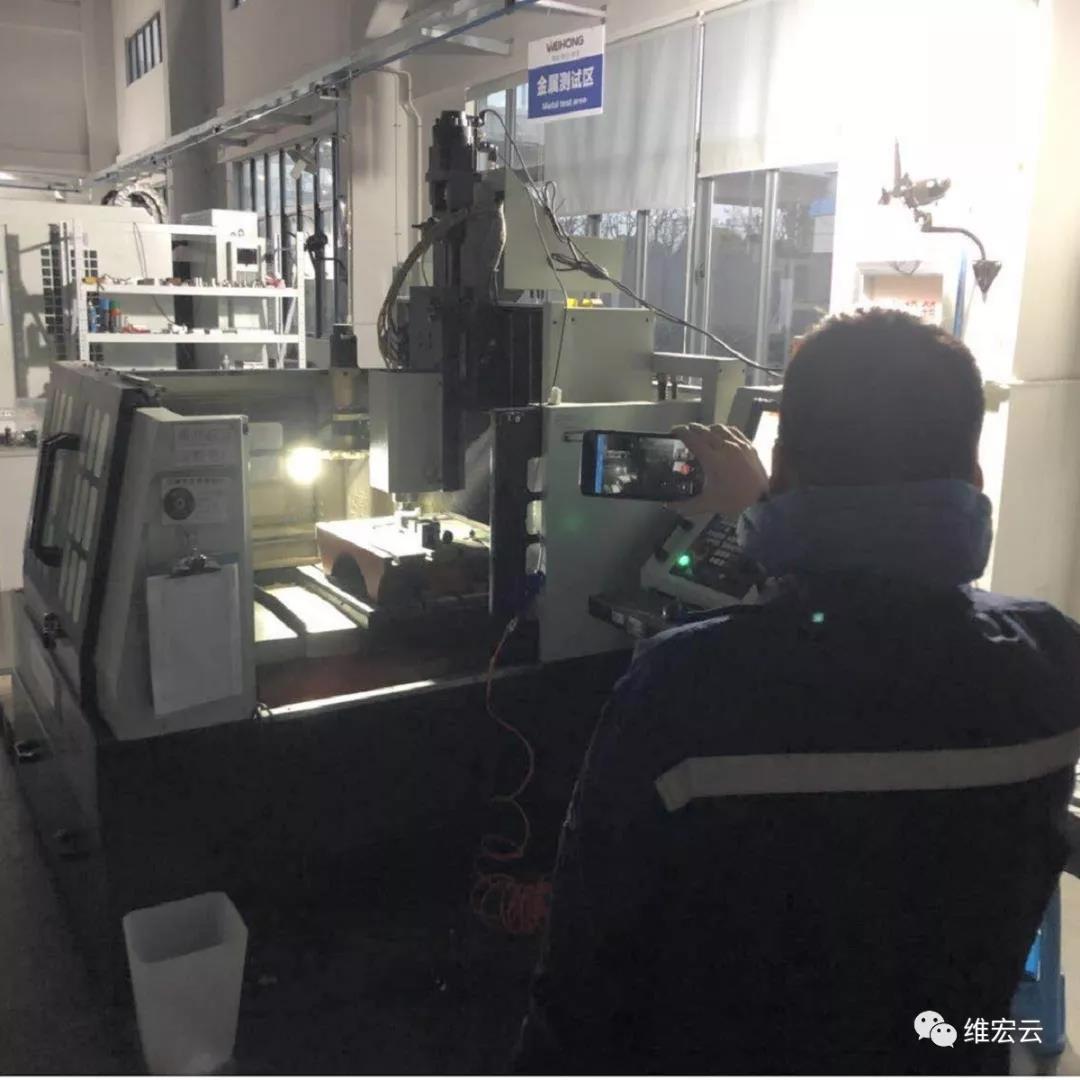
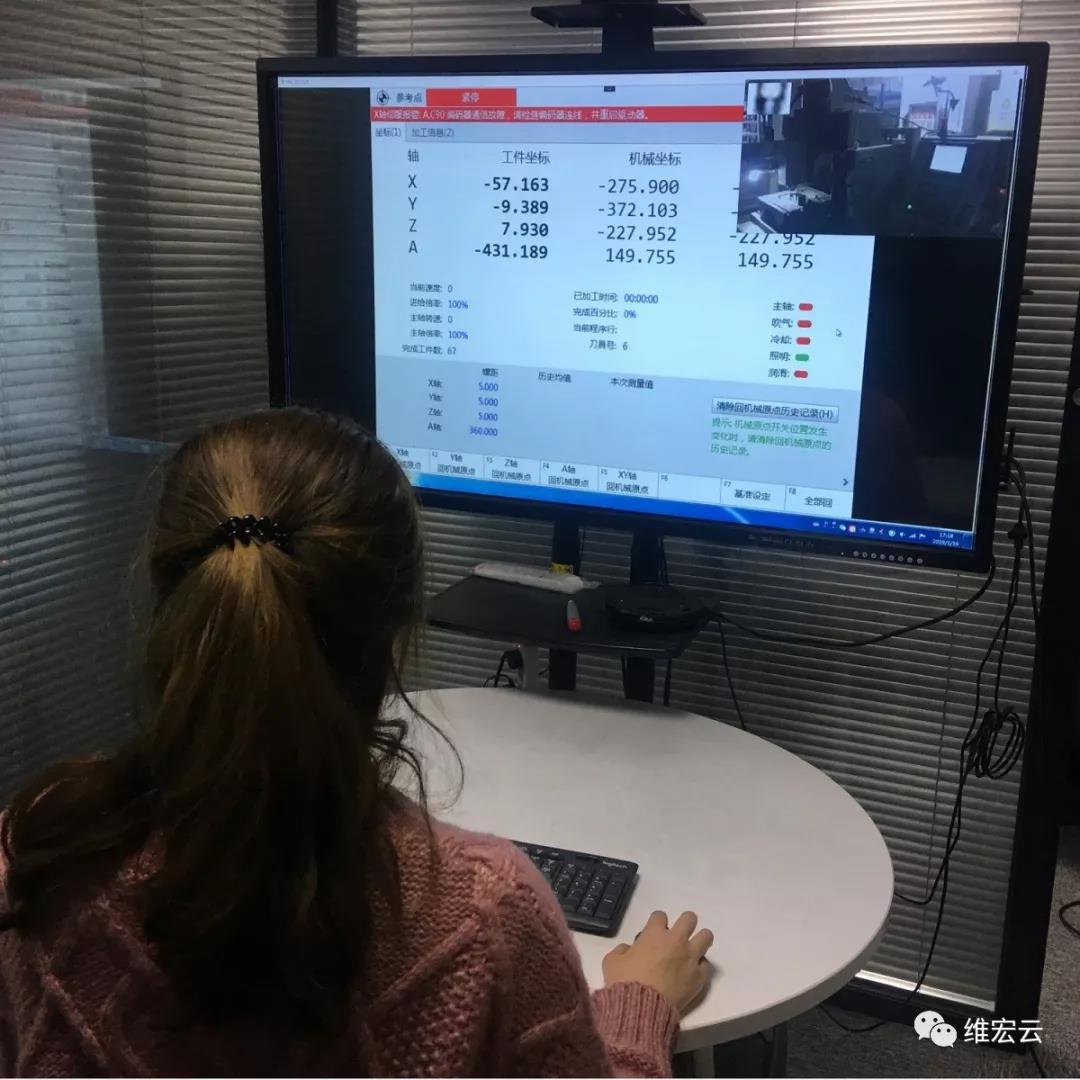
Isn’t it amazing? With a mobile phone and a computer, the remote teaching system of the machine tool was set up in one minute.
Compared with telephone or video communication, because technical support personnel can directly view and operate the machine tool, fault information and guided operations can be more direct and accurate, eliminating some unnecessary communication links. In the context of remote teaching and demonstration, you can also invite customers to remotely operate through the network and experience the operation interface and process directly. More conveniently, because the “Sunflower” remote control software supporting “Weihong Cloud-Remote Assistance” has mobile versions that support Android and Apple iOS, technical supporters can also use mobile phones to provide services anytime, anywhere. Of course, for the convenience of operation, it is recommended that the technical support personnel use a tablet with a 4G data card to achieve better results.
Utilizing the built-in “Weihong Cloud-Remote Assistance” function of Weihong CNC, in conjunction with the current popular online education live broadcast system, technician training institutions can even offer remote operation experiment courses. Imagine that a future skilled worker can just sit at a computer at home and buy a machine directly, practice the machine and become familiar with the new model. Although this method cannot completely replace on-site operator training (mainly conducive to software intervention), it can also save a lot of time and site costs for training. What benefit is it for cultivating more high-quality industrial workers!